Tin ore is an important metal ore widely used in fields such as electronics, metallurgy, and chemical engineering. The production process of tin ore refers to the process of obtaining high-purity tin metal through a series of physical and chemical treatments. This article will provide a detailed introduction to the production process of tin ore, helping readers better understand the production process of tin ore.
1、 Beneficiation of tin ore
The beneficiation of tin ore refers to the process of separating impurities and useful minerals from the raw ore. Common impurities in tin ore include quartz, Pyrite, Galena, etc. The useful mineral is cassiterite. The main purpose of mineral processing is to improve the grade of cassiterite and reduce the content of impurities.
The beneficiation of tin ore usually adopts methods such as gravity separation, flotation, and chemical beneficiation. Among them, gravity separation refers to the separation of ores by gravity according to the density difference of minerals. Flotation refers to the use of the differences in the affinity and hydrophobicity between minerals and water to separate minerals from the surface of the water. Chemical beneficiation refers to the use of chemical reactions to separate ores.
II. Smelting of Tin Ores
The smelting of tin ore is the process of high-temperature melting the processed tin ore to separate the tin metal and other impurities from it. The smelting of tin ore generally adopts two methods: electric furnace smelting and pyrometallurgical smelting.
Electric furnace smelting refers to the use of electrical energy to heat tin ore to a high temperature, causing the tin metal inside to melt and separate. Electric furnace melting has advantages such as low energy consumption and environmental protection, but its cost is relatively high. Fire smelting refers to heating tin ore and coke together to a high temperature, allowing the tin metal inside to melt and separate. The cost of pyrometallurgical smelting is lower, but it pollutes the environment.
3、 Refining of Tin Metal
The refining of tin metal refers to the further physical and chemical treatment of the molten tin metal to improve its purity. The refining of tin metal generally adopts two methods: electrolytic refining and distillation refining.
electrolytic refining refers to the process of placing tin metal into an electrolytic cell and separating impurities through the action of an electric current, thereby improving the purity of the tin metal. Distillation refining refers to heating the tin metal to a high temperature, causing impurities to evaporate and separate, thereby improving the purity of the tin metal.
4、 Processing of tin metal
The processing of tin metal refers to the process of forming and processing refined tin metal. The processing of tin metal generally includes processes such as rolling, drawing, deep drawing, and welding.
Rolling refers to heating tin metal to a certain temperature, and then pressing it into the desired shape and size through rollers. Drawing refers to heating tin metal to a certain temperature and then drawing it into the required diameter and length through a drawing machine. Deep drawing refers to the processing of tin metal into the desired shape and size, usually using a stamping machine for processing. Welding refers to the connection between tin metal and other metals, usually using Arc welding, gas shielded welding and other methods.
5、 Summary
In summary, the production process of tin ore includes processes such as beneficiation, smelting, refining, and processing. Different production processes can affect the quality and cost of tin metal, so it is necessary to choose a suitable process according to production needs. At the same time, the production process of tin ore also needs to pay attention to environmental protection and safety issues to ensure the sustainability and stability of the production process.
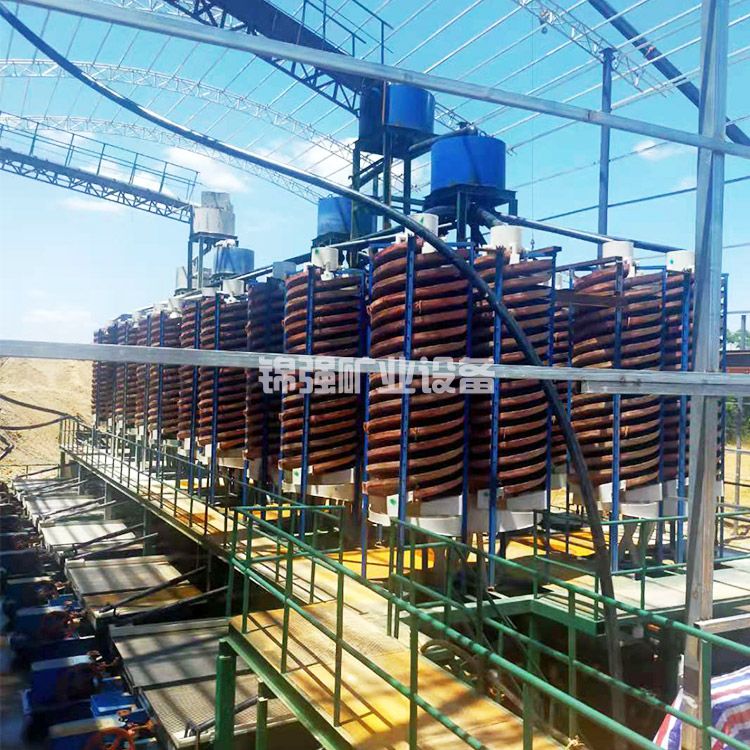