在沙金矿开采过程中,高含泥量严重影响分选效率的问题长期困扰着矿业企业。数据显示,当矿浆含泥量超过15%时,常规分选设备的回收率会下降20%-35%。要破解这一技术瓶颈,需要从系统工艺角度实施精准优化。
预处理阶段:分级洗矿降泥技术
采用三级逆流洗矿装置可将泥质含量降低至8%以下。某甘肃金矿案例显示,在滚筒筛后加装高频振动擦洗机,使-0.074mm细泥去除率提升至78%。关键要控制洗矿水压(0.3-0.5MPa)和物料停留时间(120-180秒),既保证泥质剥离又避免金粒流失。
设备改造:复合式重选系统应用
将传统溜槽改造为复合式离心分选机组,配合脉冲水流的变频控制(0.5-2Hz),可使微细金粒回收率提高12%。某内蒙矿区采用跳汰-摇床组合设备,通过调节冲程(8-12mm)和床面倾角(3°-5°),在含泥量18%条件下仍保持91.2%的回收率。
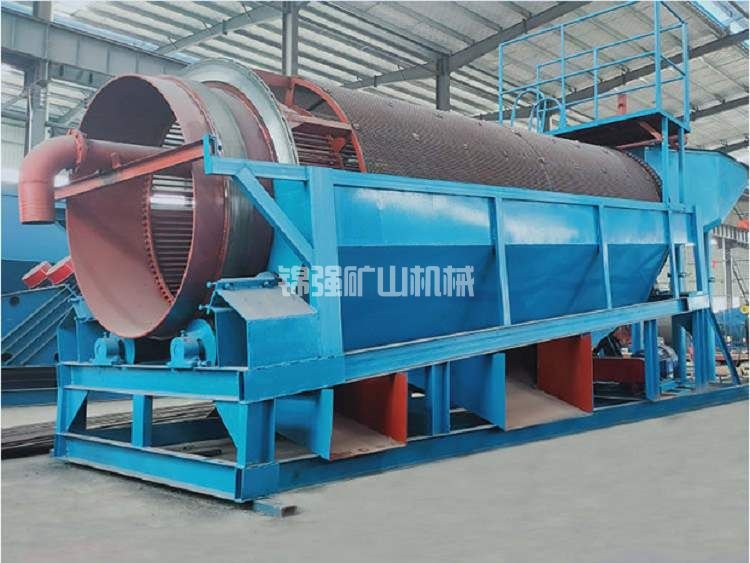
工艺优化:阶段分选浓度控制
实施三段式分选工艺:粗选(矿浆浓度35%-40%)、精选(25%-30%)、扫选(15%-20%)。云南某矿的实践表明,配合旋流器分级(分离粒度0.15mm),总回收率从82%提升至89.5%。关键要实时监测矿浆粘度(保持<30mPa·s)和PH值(6.5-7.5)。
智能分选:XRT光电技术集成
最新X射线分选机(XRT)的引入可提前分离30%-50%的废石。新疆某矿安装TOMRA矿石分选系统后,处理量提升40%,耗水量减少60%。设备通过双能X射线识别(分辨率0.5mm)和气动喷吹(0.6MPa)实现精准分选,特别适合含泥量波动大的矿体。
尾矿处理:高效脱水回收系统
配置高频脱水筛(筛孔0.075mm)+陶瓷过滤机组合,可将尾矿含水率控制在18%以下。某试验数据显示,在尾矿再处理环节增加尼尔森选矿机,可从废弃尾矿中多回收0.8g/t的金资源。关键要建立闭环水循环系统,实现每吨矿石耗水量降低至2.3m³。
行业专家预测,随着智能传感技术和流体力学模拟的进步,未来3年高泥质金矿分选效率有望突破95%大关。企业应重点关注模块化分选设备和数字孪生技术的融合应用,通过建立分选参数动态优化模型,实现全流程效率的持续提升。