Ball mill is one of the most widely used grinding equipment in the market. This equipment has a good grinding effect on the crushed materials, with a wide variety of types, including cement ball mills, energy-saving ball mills, conical ball mills, etc. Energy saving ball mills and cement ball mills are the most widely used. This article mainly compares and analyzes the differences between energy-saving ball mills and cement ball mills.
The energy-saving ball mill has changed the original mill structure, integrating the body and chassis. It can be placed on the foundation plane at once during installation. The spindle adopts double row self-aligning roller bearings, which can reduce energy consumption by 30%, increase particle size, and increase processing energy by 15-20%. Energy saving ball mills are suitable for grinding various materials such as ores, and are widely used in industries such as mineral processing, building materials, and chemical engineering. They can be divided into dry and wet grinding methods.
The cement ball mill is a continuous mill, with a lining material of cast steel and a grinding medium of cast steel. According to different discharge methods, cement ball mills can be divided into two types: grid type and overflow type. According to their application fields and efficiency, they can also be divided into ordinary cement ball mills and high fine and high yield cement ball mills.
1. Ordinary cement ball mill: Ordinary cement ball mills are mostly used in circular flow grinding systems, with high grinding efficiency, large mill output, and low power consumption, especially when grinding slag cement. The output of a regular mill can be increased by 15-20%, and the power consumption can be reduced by about 10%. In addition, the temperature of the finished product can be reduced by 20-40 ℃, and the fineness of the product can also be easily adjusted.
2. High fine and high yield cement ball mill: High fine and high yield cement ball mills are mainly used in open flow grinding systems. Its characteristics are simple system equipment and process flow, low investment, and small factory floor area; In terms of the mill structure, mature internal powder separation devices are used, and activation devices are added to the fine grinding bin. The mill tail has a dedicated discharge grate, greatly improving the efficiency of the mill and achieving the goal of high production and low energy consumption.
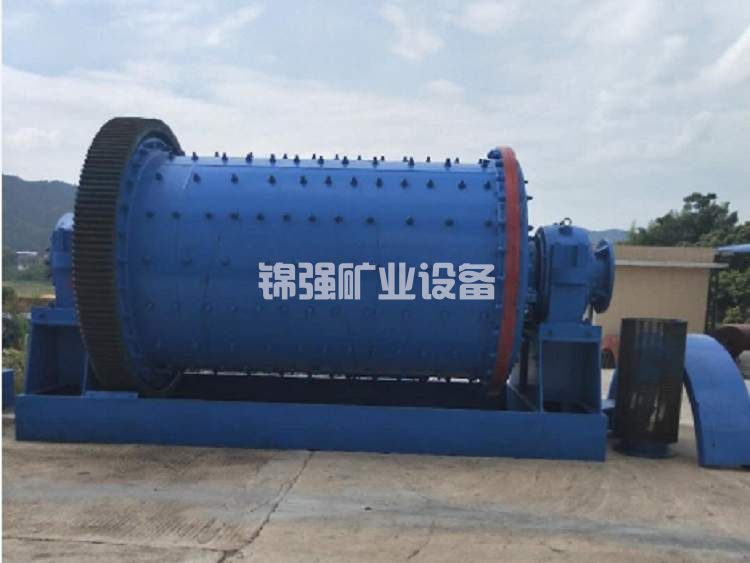
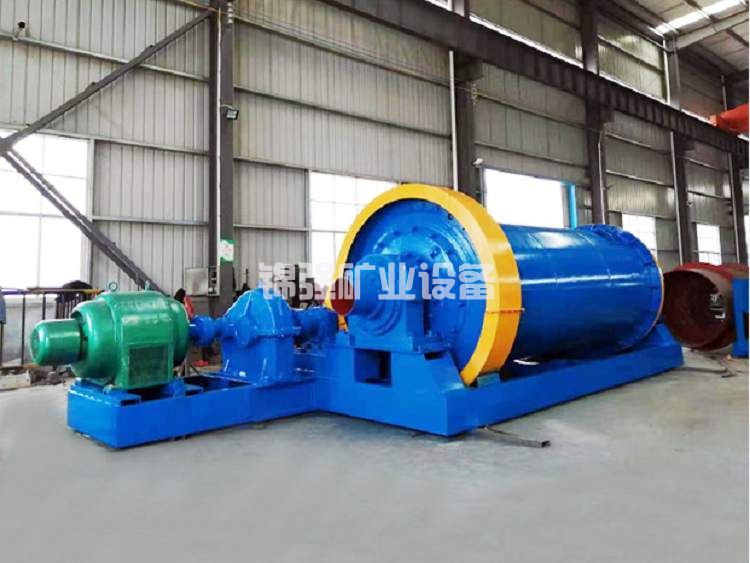
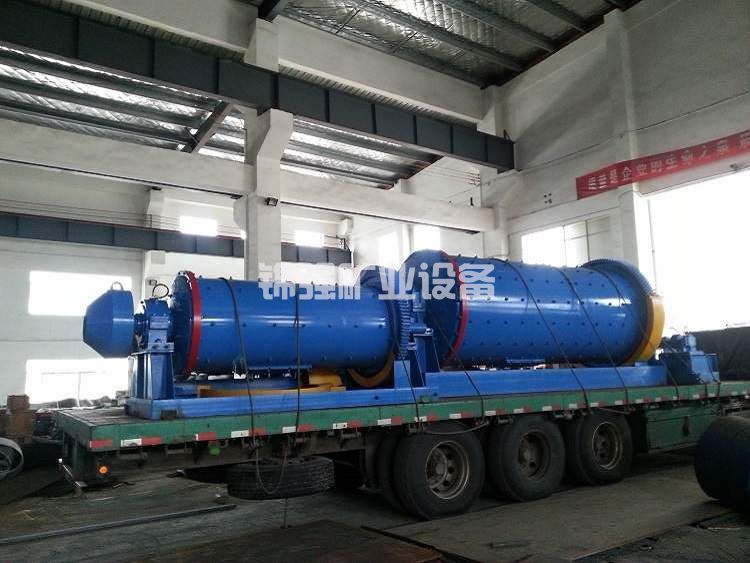
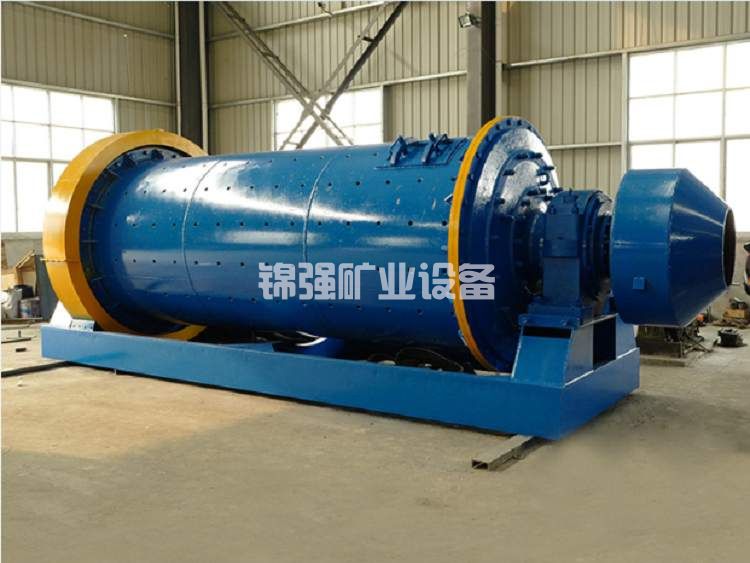
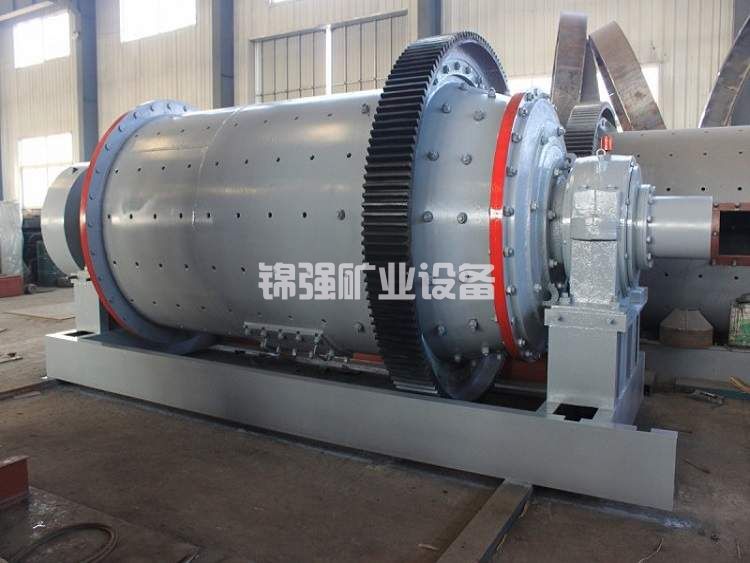