Spiral chute processing video 1 illustrates that gravity separation is widely used in the beneficiation of metal or non-ferrous metal mines due to its low environmental pollution and cost. Spiral chute is one of the gravity beneficiation machinery, with a structural feature that the cross-section presents a cubic parabolic shape, suitable for handling finer particle levels of -0.2mm. During the beneficiation process, there is no need to add water for flushing, and the tail of the chute is divided into sections to select fine, medium, and tailings. 2、 Working principle: The spiral ore separator does not need to be limited to stacking on the cross (or tripod) of the support table. The same mortar is slowly fed onto the spiral groove surface through the feeding chute installed at the beginning of the rotating groove, and selected for operation. The bottom is equipped with a valve block type equipment cutting groove, which divides the sorted products into three (or four) categories according to grade along the radial direction. Change the selection width of each equipment by adjusting the orientation of the valve block. The product gathering bucket is a concentric circular tube that enables the diverse mineral flows obtained to converge and export differently. The transverse plane of the fiberglass spiral chute and the slope of the curve change, making it particularly suitable for the selection of small particle materials. Spiral chute processing video III. Advantages and characteristics: 1. Stable, easy to operate, and wide concentration range. 2. The processing volume of mineral materials is large, with high enrichment ratio and high recycling rate. 3. It occupies a small area, consumes less water, has a simple structure, and does not require power. 4. Simple installation, easy operation, low investment, and fast returns. The structure of the spiral concentrator consists of six parts: a feeding homogenizer, a feeding trough, a spiral trough, an equipment selection trough, a product gathering hopper, and a trough bracket (including a cross or triangular frame). The spiral groove formed by connecting rotating discs is a key component. The spiral plate is made of fiberglass (fiberglass reinforced coal gangue) and connected together through screws. The sorting surface of the rotating groove has a pre designed durable wear-resistant layer. It has the advantages of lightweight, sturdy, durable, and durable consumer goods that are not easily damaged. A multi tube feeding homogenizer is installed above the rotating groove to sort minerals equally, making it easy to control. The concentrator does not need to be restricted from being placed on the cross (or tripod) of the support table. The evenly distributed slurry passes through the feeding chute installed at the head end of the spiral groove and slowly feeds onto the rotating groove surface for sorting. The tail of the spiral groove is equipped with a valve type new product acquisition groove, which allows the sorting equipment to be divided into three types (or four types) of new products along the radial direction according to grade. To adjust the orientation of the valve block and change the width of each new product, it is necessary to cut it off. The new equipment gathering bucket is a concentric annular tube that differentially collects and leads selected multi-directional mineral flows. The transverse surface of the fiberglass chute and the slope of the curve change greatly to adapt to the selection of fine-grained materials. Spiral chute processing video 5. Utilization range: Spiral chute is suitable for processing 0.6-0.03mm and vein ore or ore sand, but it is unfavorable for sorting when the mud content is high. Nowadays, it has been widely used in the processing of iron, tungsten, tin ore, niobium tantalum ore, beach and river sand mines, as well as sand gold mines.
Spiral Chute Processing Video
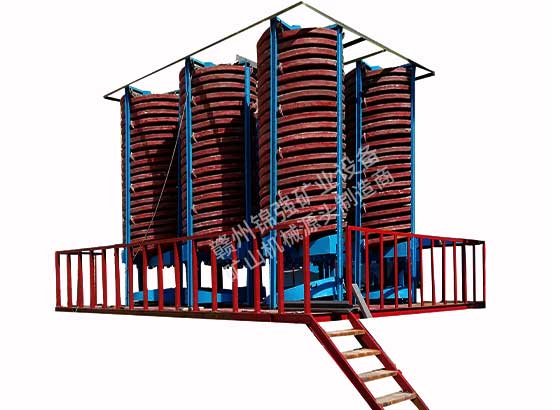