Tin is an important metal element widely used in fields such as electronics, machinery, and chemical engineering. However, the resources of tin are very limited, so the utilization of tin tailings has become particularly important. Tin tailings contain a large amount of tin, but due to their complex mineral composition and low grade, traditional beneficiation methods are difficult to obtain high-grade tin concentrates. Therefore, studying the tin tailings separation process and improving the recovery rate and grade of tin is of great significance.
Mineral composition of tin tailings
The mineral composition of tin tailings is very complex, mainly including cassiterite, Galena, Pyrite, Scheelite, quartz, mica, feldspar, Chlorite group, etc. Among them, cassiterite is the most important tin mineral in tin tailings, followed by Galena and Pyrite.
2、 Tin selection process for tin tailings
The traditional tin tailings separation process mainly includes methods such as gravity separation, flotation, and gravity flotation. Although these methods can obtain a certain amount of tin concentrate, the recovery rate and grade are relatively low, making it difficult to meet the needs of modern industry. Therefore, it is necessary to study new tin selection processes to improve the recovery rate and grade of tin tailings.
1. Gravity beneficiation method
Gravity beneficiation is a common beneficiation method. Its principle is to use the density difference of minerals for separation. For tin tailings, methods such as heavy medium separation, centrifugal separation, and spiral separation can be used. Among them, heavy medium separation is a commonly used method that can achieve high grades and recovery rates.
2. Flotation method
Flotation method is a method of separating minerals by contacting them with bubbles and allowing them to adsorb on the surface of the bubbles. For tin tailings, the forward and reverse flotation method can be used, which first uses forward flotation to obtain tin concentrate, and then uses reverse flotation to remove impurities. This method can achieve higher grades and recovery rates.
3. Hydrometallurgical method
Hydrometallurgical method is a method of separating and purifying minerals through chemical reactions in the liquid phase. For tin tailings, sodium hydroxide and sodium carbonate method, sulfuric acid leaching method, Chloride process method and other methods can be used. These methods can achieve higher grades and recovery rates, but they require higher equipment requirements and higher costs.
III. Summary
The process of selecting tin from tin tailings is a complex task that requires comprehensive consideration of factors such as mineral composition, beneficiation methods, and process flow. Currently, gravity beneficiation, flotation, and hydrometallurgy are commonly used methods that can achieve higher grades and recovery rates. In the future, with the continuous development of technology, it is believed that more and more efficient tin selection processes will emerge, providing better technical support for the utilization of tin tailings.
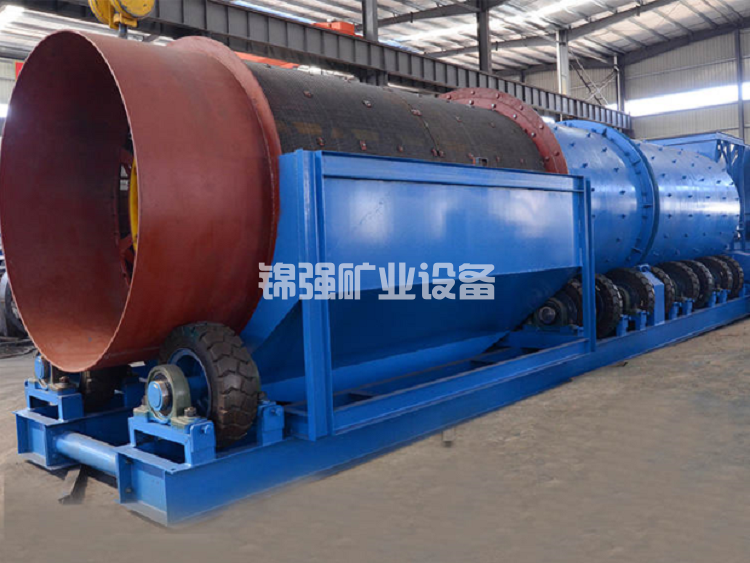